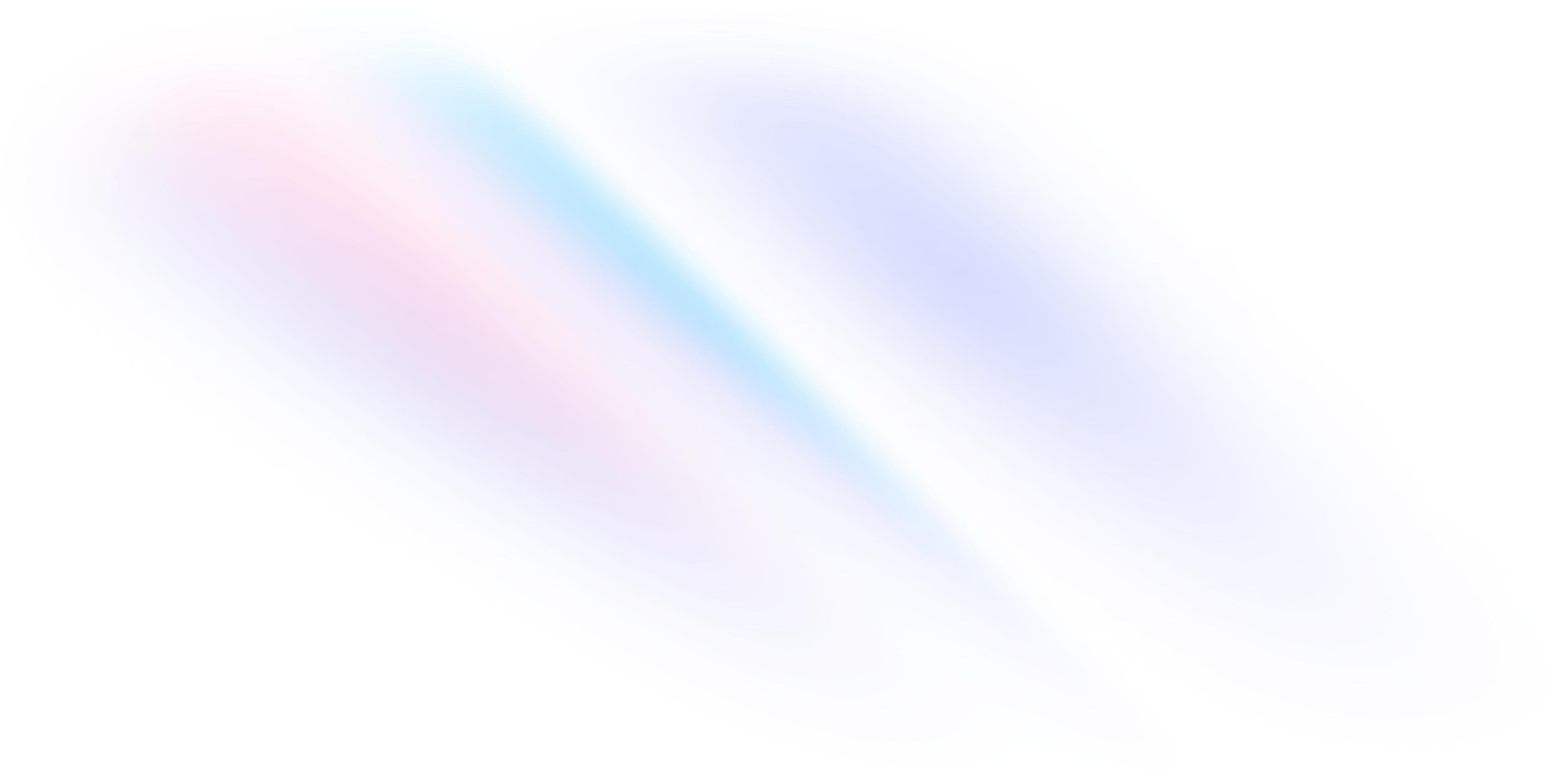
What challenges do Apparel Production Managers face?
1. Keeping up with changing fashion trends and consumer demand: Apparel production managers must stay up to date with the ever-changing fashion trends and be able to anticipate consumer demands in order to ensure their products are up to date and competitive. 2. Meeting deadlines and budget constraints: Apparel production managers must ensure that production deadlines are met and that the products are created within the budget constraints. 3. Managing a complex supply chain: Apparel production managers must manage a complex supply chain in order to ensure that the right materials are sourced and arrive in time for production. 4. Quality control: Apparel production managers must ensure that the products being produced are of the highest quality and that any defects are quickly addressed and corrected. 5. Working with vendors and suppliers: Apparel production managers must be able to build relationships with vendors and suppliers in order to ensure that the best materials are being sourced at the best prices.
Other Questions about Apparel Production Manager
- What is an Apparel Production Manager?
An Apparel Production Manager is responsible for overseeing all aspects of the production process for clothes and apparel. This includes managing staff, monitoring production processes, and working with designers to create new clothing lines. They may also be responsible for creating cost estimates, tracking inventory, and ensuring quality control standards are met.
- What experience is necessary to be an Apparel Production Manager?
Apparel Production Managers typically need a minimum of 3-5 years of experience in apparel production, manufacturing, or related industry experience. They should have a good working knowledge of production processes, quality control procedures, and garment manufacturing techniques. Experience with CAD, textile design software, and/or apparel design software is also beneficial. Knowledge of project management, budgeting, and scheduling are also important skills. Excellent communication, organizational, and problem-solving skills are essential.
- What are the typical duties of an Apparel Production Manager?
1. Develop and manage apparel production plans, schedules, and budgets. 2. Monitor production and quality control processes. 3. Hire, train, and manage staff to ensure efficient production. 4. Establish and communicate production goals. 5. Monitor labor costs and other related expenses. 6. Ensure production deadlines are met. 7. Liaise with designers, fabric suppliers, and other vendors to ensure materials and services are delivered on time. 8. Identify and troubleshoot production problems. 9. Prepare reports on production progress and related data. 10. Maintain records of production materials and processes.
- What sort of qualifications are required to be an Apparel Production Manager?
To become an Apparel Production Manager, you will need a minimum of a Bachelor's degree in a related field such as fashion design, apparel merchandising, textile science, or business administration. Additionally, you will need to have experience in the apparel industry and knowledge of apparel production processes. You may also need additional certifications or licenses, depending on the company or state you are working in.
- How much responsibility do Apparel Production Managers have?
Apparel Production Managers have a high level of responsibility. They are responsible for overseeing the day-to-day operations of the apparel production process, from the initial design stages to the final product. They are also responsible for setting budgets, scheduling production, managing personnel, monitoring quality control, and ensuring compliance with safety standards.
- What educational background is preferred for Apparel Production Managers?
Most employers prefer Apparel Production Managers to have a bachelor’s degree in a related field such as fashion design, merchandising, textiles, or business. Other helpful qualifications include experience in the apparel industry and knowledge of production processes. Many employers also prefer to hire candidates with knowledge of computer systems and software, such as Microsoft Excel.