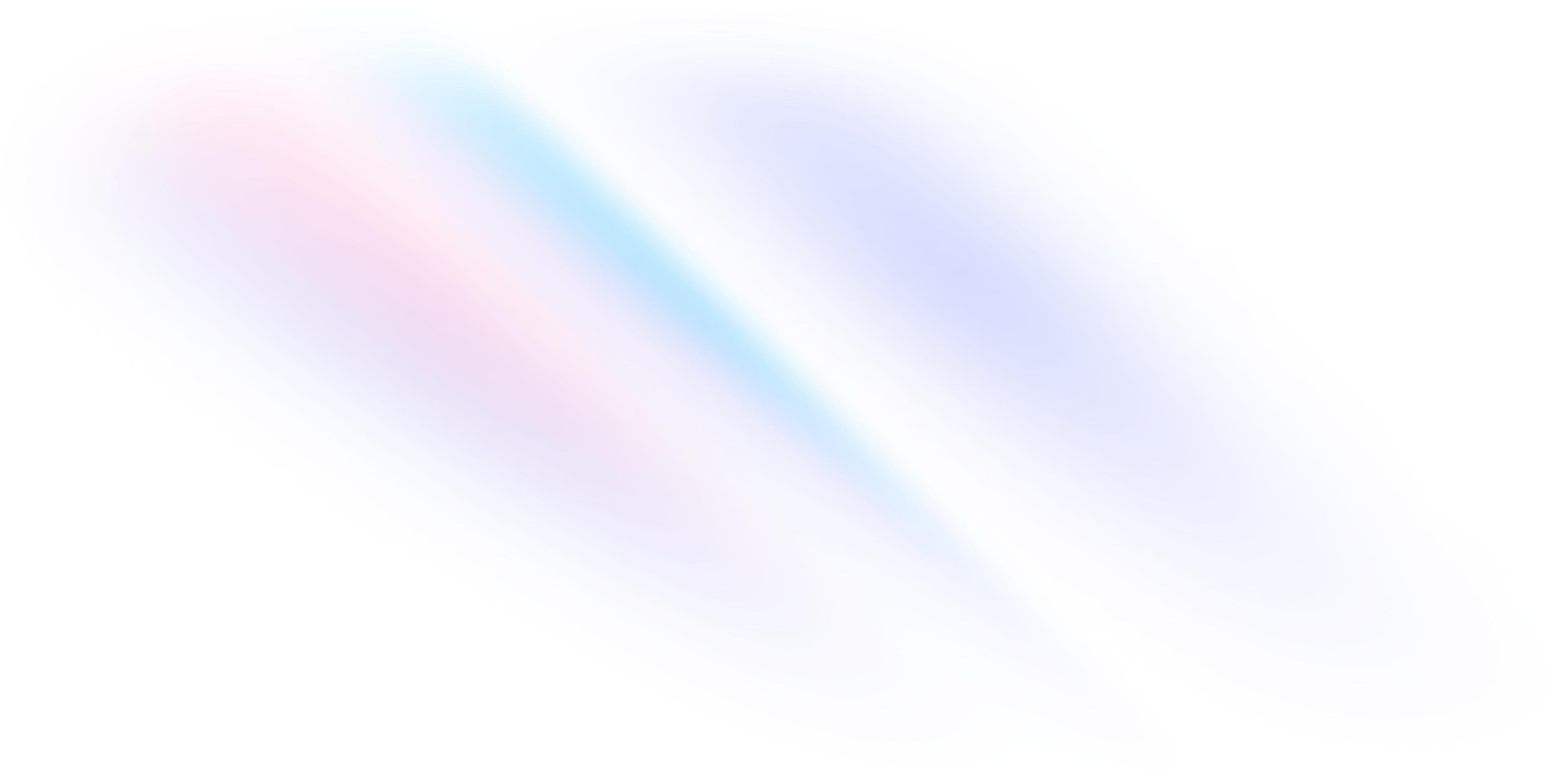
How do Apparel Production Managers manage multiple projects simultaneously?
1. Prioritize: Apparel Production Managers should prioritize their projects according to the deadlines and importance. This will help them to concentrate on completing the most important tasks first and then move on to the less important ones. 2. Delegate: Apparel Production Managers should delegate tasks to their team members to make sure that each project is completed on time and within budget. 3. Utilize Technology: Apparel Production Managers should take advantage of technological tools such as project management software to help them keep track of different projects and their progress. 4. Monitor Progress: Apparel Production Managers should regularly monitor the progress of each project to ensure that they are on track and are meeting the goals and deadlines. 5. Communicate: Apparel Production Managers should communicate regularly with their team and stakeholders to keep them updated on the progress of the projects. This will help them to stay on top of any changes or delays that may occur.
Other Questions about Apparel Production Manager
- What is an Apparel Production Manager?
An Apparel Production Manager is responsible for overseeing all aspects of the production process for clothes and apparel. This includes managing staff, monitoring production processes, and working with designers to create new clothing lines. They may also be responsible for creating cost estimates, tracking inventory, and ensuring quality control standards are met.
- What experience is necessary to be an Apparel Production Manager?
Apparel Production Managers typically need a minimum of 3-5 years of experience in apparel production, manufacturing, or related industry experience. They should have a good working knowledge of production processes, quality control procedures, and garment manufacturing techniques. Experience with CAD, textile design software, and/or apparel design software is also beneficial. Knowledge of project management, budgeting, and scheduling are also important skills. Excellent communication, organizational, and problem-solving skills are essential.
- What are the typical duties of an Apparel Production Manager?
1. Develop and manage apparel production plans, schedules, and budgets. 2. Monitor production and quality control processes. 3. Hire, train, and manage staff to ensure efficient production. 4. Establish and communicate production goals. 5. Monitor labor costs and other related expenses. 6. Ensure production deadlines are met. 7. Liaise with designers, fabric suppliers, and other vendors to ensure materials and services are delivered on time. 8. Identify and troubleshoot production problems. 9. Prepare reports on production progress and related data. 10. Maintain records of production materials and processes.
- What sort of qualifications are required to be an Apparel Production Manager?
To become an Apparel Production Manager, you will need a minimum of a Bachelor's degree in a related field such as fashion design, apparel merchandising, textile science, or business administration. Additionally, you will need to have experience in the apparel industry and knowledge of apparel production processes. You may also need additional certifications or licenses, depending on the company or state you are working in.
- How much responsibility do Apparel Production Managers have?
Apparel Production Managers have a high level of responsibility. They are responsible for overseeing the day-to-day operations of the apparel production process, from the initial design stages to the final product. They are also responsible for setting budgets, scheduling production, managing personnel, monitoring quality control, and ensuring compliance with safety standards.
- What educational background is preferred for Apparel Production Managers?
Most employers prefer Apparel Production Managers to have a bachelor’s degree in a related field such as fashion design, merchandising, textiles, or business. Other helpful qualifications include experience in the apparel industry and knowledge of production processes. Many employers also prefer to hire candidates with knowledge of computer systems and software, such as Microsoft Excel.